Einsatz künstlicher Intelligenz in der 100% visuellen Kontrolle von Parenteralia
Künstliche Intelligenz bzw. das Maschinelle Lernen haben das Potenzial, die Versorgung von Patienten im Gesundheitswesen zu verändern, indem sie neue Erkenntnisse aus den umfassenden Datenmengen gewinnen, die bei der Herstellung und Produktion von pharmazeutischen Produkten anfallen. Das Interesse der Pharma-Industrie, Künstliche Intelligenz – speziell in der visuellen Kontrolle von Parenteralia – einzusetzen, wächst aufgrund der hohen Erwartungen, bislang noch ungenutztes Optimierungspotential nutzbar zu machen, erheblich.
Die 100% Visuelle Kontrolle von injizierbaren Arzneimitteln dient der Sicherstellung der Produktqualität im Rahmen des Herstellprozess und wird durch verschiedene Arzneibücher und Guidelines (USP, Ph. Eur., EU-GMP Annex 1, etc.) geregelt.
Bislang gibt es noch keine spezifischen regulatorischen Vorgaben für die Validierung von Künstlicher Intelligenz in der Visuellen Kontrolle, was aus GMP-Sicht als problematisch angesehen werden kann. Insbesondere die Bedeutung der für das Training und die Validierung zur Verfügung stehenden Daten, des darauf basierenden Modelldesigns sowie die Sicherstellung von Qualität und Integrität der Daten über den Produktlebenszyklus hinweg, sind unklar. Validierungskonzepte werden von Regulierungsbehörden inzwischen zwar diskutiert, stehen aber noch am Anfang. Zudem herrscht bei vielen Anwendern und anderen Interessenvertretern Unsicherheit im Umgang mit der neuen Technologie.
Der vorliegende Artikel betrachtet die Unterstützung Automatisierter Inspektionsmaschinen (AIM) durch Machine-Learning-Modelle, mit dem Ziel, die Effizienz bzw. die Erkennungsleistung der Maschine zu verbessern. Dabei werden Fragestellungen rund um die Etablierung von Künstlicher Intelligenz (KI) in der regulierten Industrie, technologische Aspekte sowie ein risikobasierter Validierungsansatz erörtert. Zudem soll der Artikel einige Kriterien zur Unterstützung bei der Identifikation möglicher Anwendungsbereiche, unter Erwägung der Kosten und Nutzen, geben.
Unzureichend angepasste Anlagentechnik
Trotz aufwendiger Prüfkonzepte, wie hochauflösende Kameras und Optiken, optimierte Beleuchtungen, ausgewogene Zuführung und Präsentation der Objekte etc., arbeiten vollautomatische Visuelle Inspektionsmaschinen in technischen Grenzbereichen. Aufgrund der Variation von Prozess und Packmittel, zusätzlich zum breiten Prüfumfang, ist es häufig nicht möglich, ökonomische Interessen zu maximieren und gleichzeitig gegebene Compliance Risiken zu minimieren.
Da die Kompetenz des Lieferanten typischerweise in der Inspektionstechnologie liegt und der Kunde neben dem Herstellprozess und GMP-Compliance unmöglich auch die notwendige technische Expertise für Automation und Anlagenbau mitbringen kann, werden vollautomatische Inspektionsmaschinen schon im Rahmen von Beschaffungsprojekten häufig unzureichend spezifiziert. Die ungenügend an den Herstellprozess angepasste Inspektionsmaschine kann unter realen Bedingungen folglich nur mit großen Verlusten (aufgrund von False-Rejects) betrieben werden. Für den Kunden beginnt damit ein mitunter über Jahre hinweg andauernder Optimierungsprozess.
Neue Möglichkeiten durch den Einsatz von KI
Künstliche Neuronale Netze sind Algorithmen, die dem menschlichen Gehirn nachempfunden sind. Ein abstrahiertes Modell von verbundenen künstlichen Neuronen ermöglicht es, komplexe Aufgaben aus den Bereichen Statistik, Informatik und Wirtschaft durch Computer zu lösen. Dabei lassen sich verschiedene Datenquellen wie Bilder, Geräusche, Texte, Tabellen oder Zeitreihen interpretieren und Informationen oder Muster extrahieren. Angewandt auf neue Prozessdaten lassen sich so Vorhersagen für die Zukunft erstellen.
Nach dem derzeitigen Stand kann auch die Automatisierte Visuelle Inspektion (AVI) durch den Einsatz von Künstlicher Intelligenz erheblich profitieren, indem Inspektionsrezepte schneller für den kommerziellen Einsatz bereitgestellt und zugleich die Unterscheidung zwischen akzeptablen und nicht akzeptablen Einheiten verbessert wird.
Die Erstellung eines Machine-Learning-Modells
In der Visuellen Kontrolle gilt der Mensch bis heute als der "Gold-Standard", da er - zumindest über begrenzte Zeiträume und Volumina hinweg - gleichmäßig zuverlässige und hochwertige Ergebnisse liefert. Um die Entscheidungsstrukturen des Menschen nachzubilden, entwickelt man künstliche neuronale Netze (KNN), deren Komplexität bzw. Topologie in Abhängigkeit zur Inspektionsaufgabe entsprechend "angepasst" werden muss.
Künstliche neuronale Netze werden in Schichten bzw. Ebenen unterteilt. Beim Entwurf gilt es in einer gegebenen Familie von neuronalen Netzen jenes zu finden, welches gut an die Bedürfnisse der Prüfaufgabe angepasst sowie gleichzeitig effizient und ressourcenschonend genutzt werden kann. Nach der Festlegung der Architektur folgt die Trainingsphase, in welcher das Netz mit Ein-Ausgabe-Datenpaaren trainiert wird.
Ein Datenpaar besteht in unserem Beispiel aus dem Bild eines Produkts (Eingabe) und dem erwarteten Ergebnis (Ausgabe). Die Zuweisung des Ergebnisses zu einem Bild erfolgt beim „supervised learning“ durch menschliche Interaktion im Rahmen des „Labelings“. Die so durch Menschen (der sogenannte „Human-in-the-Loop“ - HITL) überwachte Qualität des Datensatzes stellt sicher, dass das Netz die richtigen Entscheidungen trifft.
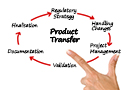
Seminarempfehlung
Barcelona, Spain16-18 September 2025
Product Transfer
Durch Training und Validierung des Netzes wird eine Funktion erzeugt, die neue Varianten bzw. Bilder des Produkts idealerweise korrekt erkennt und das richtige Ergebnis zuordnet. Die Abstraktion eines solchen Netzes wird häufig auch als „Modell“ bezeichnet.
Fig. 1: Herausforderungen
Das Modell ist dann gut angepasst und kann für den Einsatz im regulierten Umfeld eingesetzt werden, wenn es über die in den Trainingsdaten repräsentierten Ausprägungen hinaus robust und wiederholbar verallgemeinern kann.
Herausforderungen
Bisher werden Rezepte für Inspektionsmaschinen durch Vision- Techniker erstellt. Die Erstellung und Überwachung der ordnungsgemäßen Funktion basiert auf den zur Verfügung stehenden Trainings- und Qualifizierungssets. Die Eignung und Leistung der Maschine im Alltag ist maßgeblich von der Kompetenz und Expertise des Vision-Experten bei der Anpassung des Rezepts abhängig. Darauf folgt die Optimierungsphase. In der Regel ein kontinuierlicher Prozess, der im Rahmen des Life-Cycle-Managements eingeplant und nachgehalten werden muss. Glaubt man den Diskussionen um die scheinbar unbegrenzten Einsatzmöglichkeiten, mag man denken, dass die Künstliche Intelligenz den Experten zukünftig ersetzten und Probleme dieser Art selbstständig lösen könnte. In der Realität funktioniert dies aber ebenso wenig wie die Beschaffung einer Inspektionsmaschine ohne Expertenwissen.
Ein Riss ist im Bild der Kamera häufig nur schwer von einem Artefakt, also einer durch die Optik hervorgerufenen Bildstruktur (Reflexion, Unschärfe, etc.), zu unterscheiden (siehe Bild „Herausforderungen“). Gerade bei Grenzmustern, also Einheiten, die sich anhand des Bildes nicht durch eindeutige, „starke“ Merkmale unterscheiden lassen, wird es schwierig bis unmöglich, das Produkt korrekt zu klassieren. Da der normale Anwender typischerweise aber kein Experte für das Verstehen von Bildern ist und der Data Scientist in der Regel keine Erfahrung in Prozess- und Produktwissen mitbringt, können diese Herausforderungen nur dann zufriedenstellend adressiert werden, wenn man es schafft, zwischen beiden Parteien zu vermitteln, um gegenseitiges Verständnis zu schaffen.
Im ungünstigsten Fall wissen weder der Anwender noch der Datenwissenschaftler, dass der Algorithmus auf unvollständigen, nicht repräsentativen Daten entwickelt wurde und so möglicherweise Compliance Risiken unentdeckt bleiben. Dies gilt für die Abstraktion von Modellen bei regelbasierten, traditionellen Klassifikatoren, wie auch im Kontext des maschinellen Lernens, bei der der Data Scientist die verfügbaren Bilder zu Datensätzen formt, um damit das Modell zu trainieren. Zur Illustration und dem besseren Verständnis siehe Bilder zur Erstellung und Leistung eines Modells (Schritte 1-4).
Fig. 2-5: S 1-4
Vergleichbar mit dem Lernprozess des Menschen muss auch das Modell im Rahmen des Überwachten Lernens mit speziell erstellten und ausbalancierten Datensätzen trainiert und validiert werden, wobei der Umfang von der Informationsqualität der Daten und den Fehlerkosten der Anwendung abhängig ist.
Risiken der Künstlichen Intelligenz
Das Risiko eines Machine-Learning-Modells ist grundsätzlich abhängig von dem Einsatzbereich und den damit verbundenen Kosten einer falschen Entscheidung. Bei der Visuellen Kontrolle sollte die Kritikalität des Herstellprozesses, an dem das Modell beteiligt ist, das inhärente Risiko des Arzneimittels, wie zum Beispiel Anforderungen an die Sterilität, sowie optional zusätzlich vorhandene Überwachungen, wie die stichprobenartige Nachkontrolle (AQL), berücksichtigt werden.
Neuronale Netze identifizieren Muster in Trainingsdaten und nutzen diese für die Vorhersage von zukünftigen Daten. Vergleichbar zum Menschen, die, emotional geprägt, dazu neigen, Informationen so zu interpretieren, dass die bisherige Ansicht bestätigt wird („confirmation bias“), verhält es sich auch beim Maschinellen Lernen.
Unausgewogene, unspezifische Trainingsdaten beispielsweise können dazu führen, dass irrelevante Strukturen durch Überanpassung fokussiert („Overfitting“) oder die Ausrichtung des Modells auf dominante Merkmale („Biasing“) gefördert werden. Sind dagegen relevante Muster in den Trainingsdaten nicht hinreichend repräsentiert, spricht man von Unteranpassung („Underfitting“). In beiden Fällen erlauben die aus den Daten gewonnenen Annahmen keine zuverlässigen Rückschlüsse auf die Wirklichkeit.
Während bei der Entwicklung und dem Training von Modellen die zuvor gennannten, datenwissenschaftlich getriebenen, Risiken („model risks“) zu berücksichtigen sind, erkennen immer mehr Unternehmen, dass die Pflege des Modells im Life-Cycle eine ebenso große, wenn nicht noch größere, Rolle spielt.
So kann die unvollständige Dokumentation und Verwaltung der in der Produktion eingesetzten Modelle und damit verbunden das fehlende Wissen, welche Daten bei der Erstellung des jeweiligen Modells genutzt wurden, zu Datenintegritätsrisiken führen: Modelle, die in der Vergangenheit erstellt wurden, entsprechen nicht den aktuellen organisatorischen Anforderungen für Tests und Dokumentation. Oder Abhängigkeiten zwischen den Modellen in der Produktion werden nicht erkannt, oder die unzureichende Überwachung der Modelle im Life-Cycle führt zu einer Verschlechterung der Leistung, um nur einige zu nennen.
Risikominimierung
Technische Risiken, die aus dem Design, dem Training und der Validierung einhergehen, nehmen unmittelbar Einfluss auf die Sicherheit und Leistung des Modells. Diese Risiken können vermieden bzw. kontrolliert werden, wenn über den gesamten Lebenszyklus hinweg umfassendes Domänen-Wissen zur Verfügung gestellt werden kann. Um eine angemessene Leistung des Modells für die Zielanwendung zu fördern, etwaige Verzerrungen oder Fehler zu vermeiden und Umstände vorherzusagen, unter denen das Modell möglicherweise unterdurchschnittlich abschneiden könnte (z. B. bei Datensatzdrift), müssen Eigenschaften und Variationen von Produkt und Herstellprozess in den Trainings- und Validierungsdatensätzen ausreichend repräsentiert sein.
Da die zur Verfügung stehenden Trainings- und Qualifizierungssets meist künstlich hergestellt werden, deren Anzahl limitiert und so die Repräsentativität im Vergleich zur Realität der Produktion begrenzt ist, sollten die daraus erstellten Datensätze fallweise durch Daten aus der Produktion wie auch durch künstliche Daten angereichert werden. Der Zusammensetzung und Qualität solcher „Referenzstandards“ kommt aus GMP-Sicht eine besondere Bedeutung zu und sollte neben der Erstellung, Qualifizierung und Betreuung der Neuronalen Netze im Life-Cycle Risiko basiert geregelt und in entsprechenden SOPs festgehalten werden.
Prozessseitig kann eine Strategie zur Verwaltung von Modellen, den ALCOA-Grundsätzen folgend, helfen, die Zuordnung, den Einsatzbereich und die Verwendung der Modelle zu beschreiben, regelmäßig nachzuhalten und damit die Rückverfolgbarkeit zu gewährleisten.
Etablierung und Qualifizierung eines Modells im Life-Cycle
Der Lebenszyklus („Life Cycle“) eines „Modells“ kann in fünf Phasen unterteilt werden:
Identifikation möglicher Optimierungsbereiche
Der erste Schritt im Lebenszyklus eines Modells ist die Erkennung, Analyse und Beschreibung des Optimierungsbedarfs („Identify“). Die Auslöser für die Neuerstellung bzw. Änderung eines Modells lassen sich grundsätzlich in geplante und ungeplante Ereignisse unterscheiden:
Einführung oder Optimierung von Modellen im Rahmen geplanter Änderungen:
Bei Neuanschaffung einer Inspektionsmaschine, begleitend zu Produkttransfers oder durch Etablierung neuer Kontrollprozesse ausgelöste Änderungen, sowie Änderungen, die zur Steigerung der Effizienz, Funktion oder der Robustheit bestehender Prozesse vorgeschlagen werden.
Ungeplante Änderungen im Rahmen von Qualitäts- und Compliance-Ereignissen:
Änderungen, die wegen eines Qualitäts- oder Regelkonformitätsereignisses (z. B. nach Abweichungen, CAPAs oder Behördenanforderungen) nötig werden. Hierzu zählen z.B. systematisch übersehene Defekte, die im Gutstrom nachgewiesen wurden (z.B. AQL-Test).
Anforderungsspezifikation
In der Spezifikationsphase werden das Problem und die Anforderungen erfasst und dokumentiert. Dazu gehören Produkt-, Darreichungsform- und Packmittel-Spezifikationen, Eigenschaften der Maschine (Typ, Inspektionsstationen, Geschwindigkeit, etc.), Anforderungen an die Produktqualität (z. B. Defekte und deren Priorisierung nach Kritikalität) und Herausforderungen bei der Klassifizierung von Fehlerbildern, wie zum Beispiel bei Mehrdeutigkeiten aufgrund der fehlenden Unterscheidbarkeit von Mikroblasen, Partikeln oder anderer Artefakte, also jene Grenzfälle.
Im Rahmen der Benutzeranforderungen müssen auch die benötigten Datensätze spezifiziert werden. Künstlich hergestellte Muster, wie Qualifizierungssets, bilden die Grundlage. Darüber hinaus braucht es realistische Daten aus der Produktion, welche durch künstliche Daten angereichert, den "Reality-Gap" schließen sollen.
Sobald die ersten Daten erfasst und das Inspektionsproblem verstanden wurde, sollten zwischen Anwender und Lieferant des Modells eine Labeling-Guidance vereinbart, kommuniziert und für die Mitarbeiter des Labeling-Teams verfügbar gemacht werden.
Erstellung, Training und Validierung des Modells
Basierend auf den zur Verfügung gestellten und gekennzeichneten Datensätzen, folgt das Design, Training und die Validierung des Modells. Damit mögliche Auswirkungen auf die Sicherheit und Leistung des Modells kontrolliert werden können, gilt es, die gleichsam aus der traditionellen Bildverarbeitung bekannten „Model-Risks“ zu berücksichtigen (siehe Abschnitt „Risiken der Künstlichen Intelligenz“).
Trainings- und Validierungsdatensätze müssen so ausgewählt und verwaltet werden, dass über den gesamten Prozess hinweg sichergestellt ist, dass sie entsprechend unabhängig voneinander sind. Bei der Erstellung von Datensätzen sind alle relevanten Informationen zur eindeutigen Kennzeichnung und Unterscheidung zu erfassen und zu dokumentieren (z. B. Maschine, Produkt, Kamerastation, Kennzeichnung bzw. Nummerierung des Musters, Beschreibung der objektiven Beurteilung eines Musters, wie z. B. Gut- / Schlecht bzw. Produktionsware).
Qualifizierungsstrategie
Nach der Bestätigung der erwarteten Funktion im Rahmen der Validierung wird das Modell „eingefroren“ und die Erkennungsleistung mit den zur Verfügung stehenden Qualifizierungssets an der Maschine bestätigt. Dieser Schritt sollte der Vergleichbarkeit und Erklärbarkeit wegen analog zu den traditionellen Verfahren durchgeführt werden, auch wenn die künstlich hergestellten Qualifizierungssets nicht notwendigerweise aussagekräftig für die Bestätigung der Leistung sind.
Mindestens genauso wichtig aber ist die Sicherstellung und Dokumentation, dass die risikobasierten Vorgaben zur Erstellung des Machine-Learning-Modells eingehalten wurden und damit im Einklang mit den genehmigten „Good-Machine-Learning Practises (GMLP)“ stehen (siehe Abschnitt „Risikominimierung“. Wie zuvor bereits mehrfach darauf hingewiesen, sollte der Zusammenstellung und der Repräsentativität der Trainings- bzw. Validierungsdaten dabei eine besondere Bedeutung beigemessen werden.
Betrieb
Nach der Qualifizierung des eingefrorenen Modells empfiehlt es sich, die ordnungsgemäße Funktion des Modells, auch zur Förderung des Vertrauens und möglicher neuartiger Erkenntnisse, im Rahmen der regulären Herstellung zu verifizieren. Das ordnungsgemäße Verhalten und die finale Freigabe des KI-gestützten Rezepts könnten zum Beispiel im Rahmen der Prozessvalidierungschargen bestätigt werden. Auch der Vergleich des traditionellen (nicht KI-gestützten) Rezepts mit der Entscheidung des Machine-Learning-Modells im Rahmen eines Benchmarkings kann Vertrauen in die neue Technologie fördern.
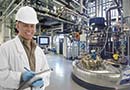
Seminarempfehlung
23.-25. September 2025
Pharma-Ingenieur/in (PT 25) - Block I - Live Online Seminar
Entlang des Lebenszyklus sollten zuvor geregelte Maßnahmen zur kontinuierlichen Überwachung und Pflege von Modellen wie auch zur Erweiterung des datengetriebenen Prozessverständnisses nachgehalten und damit die oben genannten Risiken abgewendet werden.
Fazit
Unterstellt man dem Beitrag der Visuellen Kontrolle zum Herstellprozess in Kombination mit der hohen Komplexität bzw. Mehrdeutigkeit der Daten ein mittleres bis hohes Risiko, müssen für die Erstellung eines Modells pro Kamerastation typischerweise bis zu 30.000 gekennzeichnete Daten zur Verfügung gestellt werden. Selbst einfache Anwendungen mit geringem Risiko benötigen realistischerweise noch immer Datensätze mit 1.000 oder mehr Einträgen.
Auch wenn die Integration und Qualifizierung KI-gestützter Systeme zunächst mit hohem Aufwand verbunden und die Risiken noch nicht in der breiten Masse verstanden sind, führt die strukturierte Sammlung und Sichtung von Daten zu einem sich "kumulierenden" Prozess- und Produktwissen", welches auf weitere Produkte und Anwendungen übertragen werden kann. Durch den Einsatz von Technologien wie dem Transfer-Learning kann die heute übliche Entwicklungs- und Inbetriebnahmephase für neue Rezepte und Prozesse deutlich verkürzt und darüber hinaus auch im Sinne der Qualität standardisiert werden.
Wer hohe Anforderungen an die Produktqualität (geringe "False-Acceptance-Rate") und gleichzeitig an die Effizienz (geringe "False-Reject-Rate") des Inspektionssystems hat, braucht ein Konzept, wie das Produkt-spezifische Wissen kontinuierlich in die Optimierung der Algorithmen einfließen und über lange Zeit für das Unternehmen nutzbar gemacht werden kann.
Autor:
Felix Krumbein
... war bei Roche verantwortlich für die Entwicklung von Konzepten rund um die Qualifizierung von Inspektionsmaschinen. Bei InspectifAI leitete er den Bereich Visual Inspection für die Entwicklung KI-gestützter Lösungen für vollautomatische Inspetionsmaschinen. Herr Krumbein ist Head der ECA Visual Inspection Group.